Engineering
Jigs & Trim Fixtures
High quality fixturing is essential for systematising product manufacture – speeding up processes, ensuring consistent quality and increasing efficiency. The best fixture design relies on a combination of truly understanding what the customer is trying to improve and working out a clever but simple solution to the issue. This needs to rely on detail of the step by step process the fixture will support, considerations for ease of use for the operator and if one fixture can deliver the complete solution or if multiple operations are needed.
Explore Our Jigs & Trim Fixture Capabilites
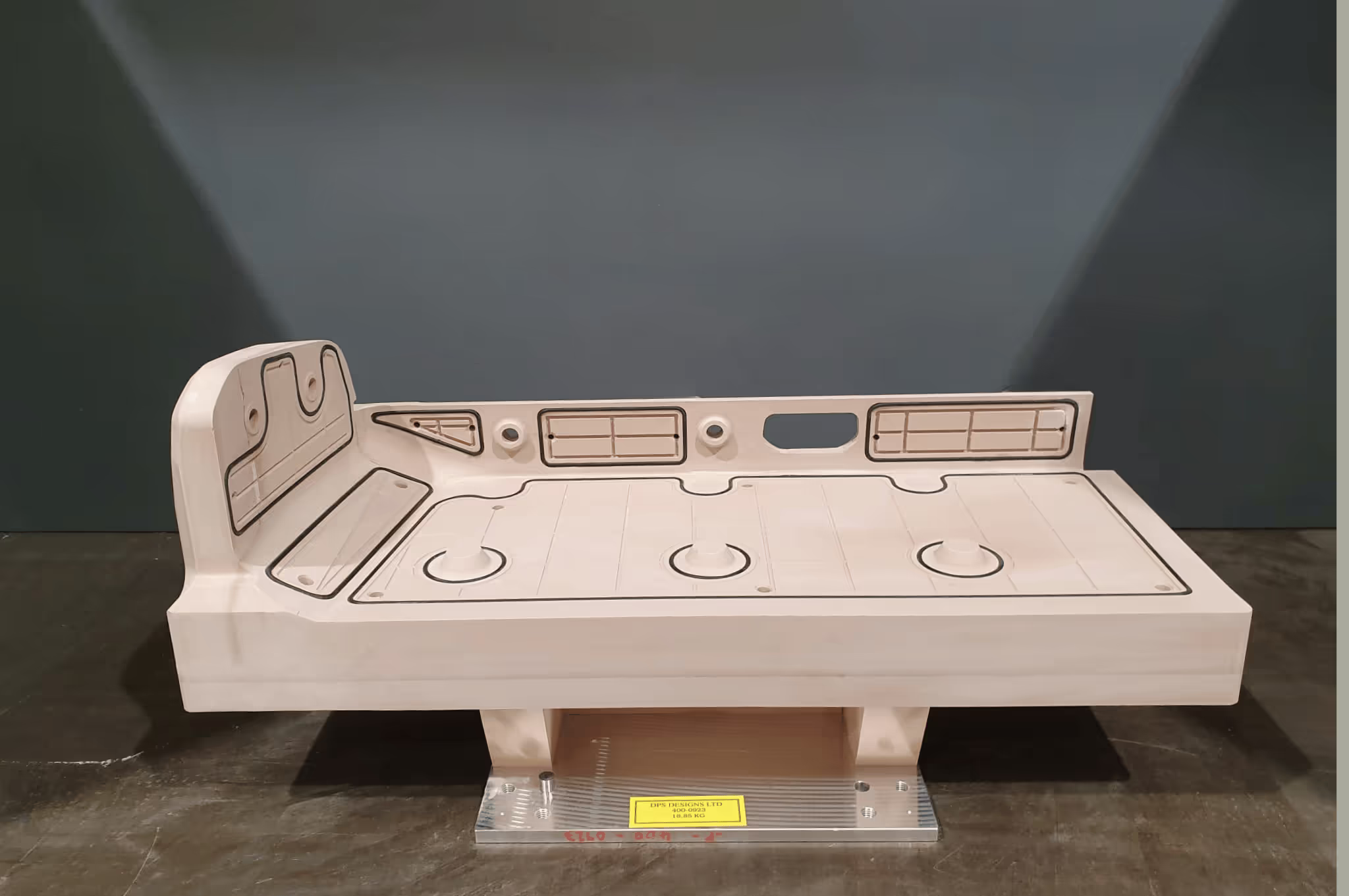
This is the main stay of our fixturing work – holding plastic parts securely using vacuum so that they can be trimmed on a 5-axis router. As part of our team we have people who have spent time operating trimming machines so we can anticipate future real-world potential problems and design them out in advance. Sometimes this will need us to take a change of approach in the mould tool before we even get to the fixture.
All fixtures are made according the needs of your process and machine standards for location and vaccum. They are cut relative to dowels in their base plate so they can fit on your machine, be offline programmed and the cutter will go exactly to where it needs to, saving you considerable down time.
.avif)
Waterjet fixturing is a relatively specialist expertise that DPS has developed over time yet it’s critical for cutting parts that cannot be trimmed conventionally.
Special attention needs to be given to holding the part and scrape area, how to allow water to pass through the fixture and how to baffle that water for any internal cuts that could otherwise cut right through the component.
We have developed a process for quickly and efficiently manufacturing waterjet fixtures which are CAD-cut – not reliant on GRP – and are therefore both dimensionally spot on and can be up-issued if needed without the need for a new fixture.
.avif)
The challenges of fixturing for cutting by laser is similar to water but different. The laser doesn’t need to pass through the fixture in quite the same way but it does need to be baffled to stop it cutting through other areas of the component and consideration needs to be given to smoke extraction.
Sonic welding can often have a very tight tolerance and as such the fixturing needs to be really accurately made. The fixtures will often have to have careful thought towards how the often-smaller component will be held firmly to be welded to the larger component and this design can be make or break for if a good quality weld is achieved. We have a long track record of achieving successful result for a reliable and repeatable weld.
.jpg)
Die cut tools can be a very cost effective way of quickly and simply cutting flat parts to size. Importantly, achieving location of the untrimmed parts for die cutting needs to be though through during the mould tool design phase.
Working with trusted partners to produce the bent knives themselves we’ve been designing and delivering die cut tools for 20 years. We can supply anything from relatively simple tooling with short knives right up to deep serrated knives with a top and bottom tool to give a shaped, fully supported cut. We often help customers to die cut parts initially thought not to be possible, removing the need for waterjet cutting which is slower and more expensive.
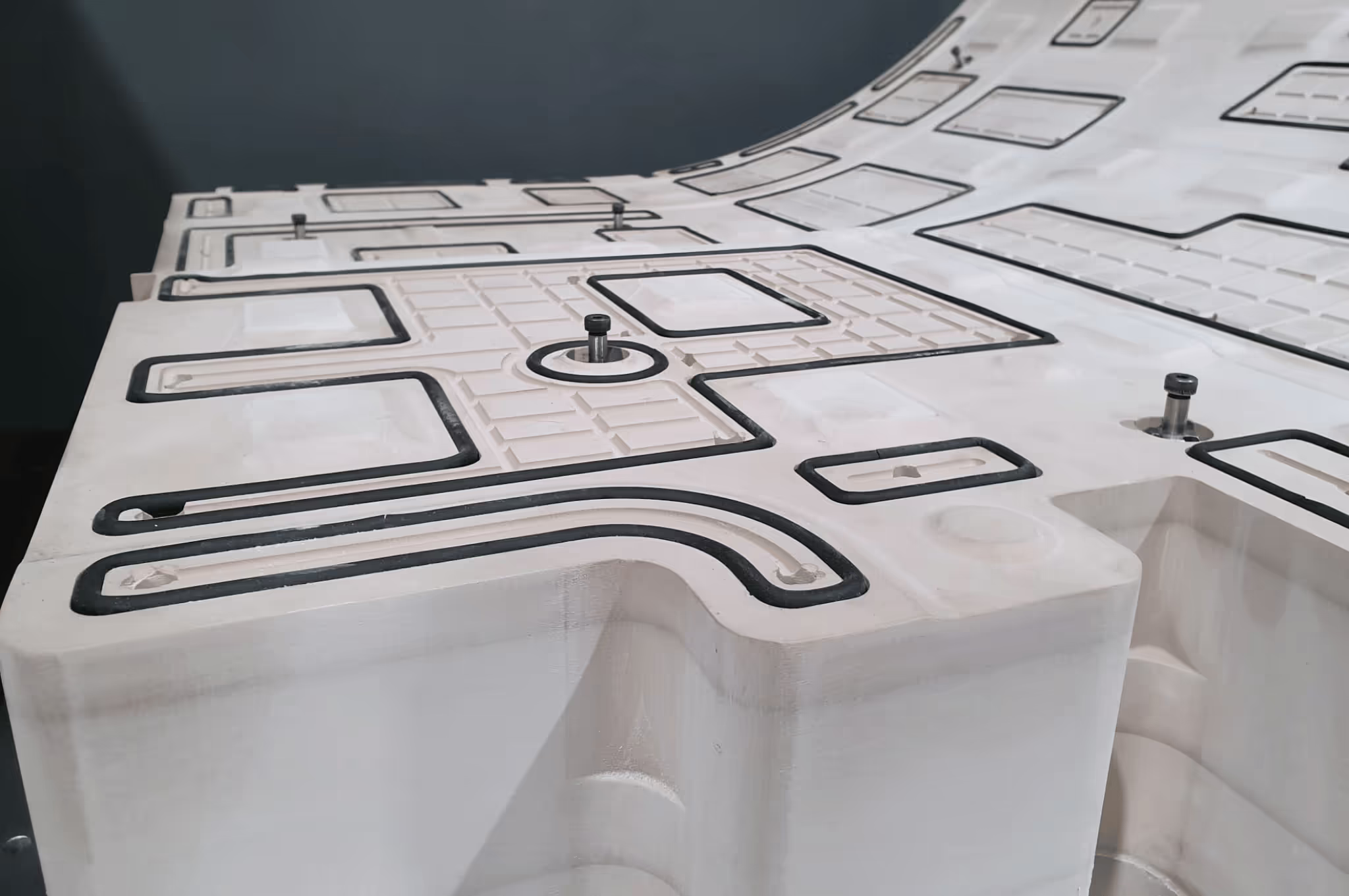
Composite fixtures can be extremely exacting in terms of tolerance due to how rigid the composites themselves are, there is often simply no flex in them. We are well used to working with these tight tolerances even with softer model board material used for fixturing.
Special consideration also needs to be taken in design as to how the parts will be held where vacuum is concerned. We are happy manufacturing fixturing both for composites coming off tooling we have made and where the tooling for the manufacture of the composites have been done elsewhere. We will simply either work with CAD supplied of the component, or reverse engineer the jig from the finished component.
.avif)
Checking fixtures can be an extremely broad church – from simple fixtures with a tolerance band to aid a visual quality check through to a POKE OKE fixture that locks in and doesn’t release a part that is out of tolerance until a supervisor releases it.
Our approach to fixture design is to understand the tolerances needed, the specific areas to check and the level of risk associated with the component when in use. We will always focus on creating a solution that is as simple as possible in order to be fit for purpose.
We provide verification reports with all fixturing whereby we 3D scan the fixture and use industry-leading software to compare what has been manufactured to the CAD. This gives customers peace of mind but is also often needed for their own quality processes. We’re also happy for our fixturing to be externally verified.
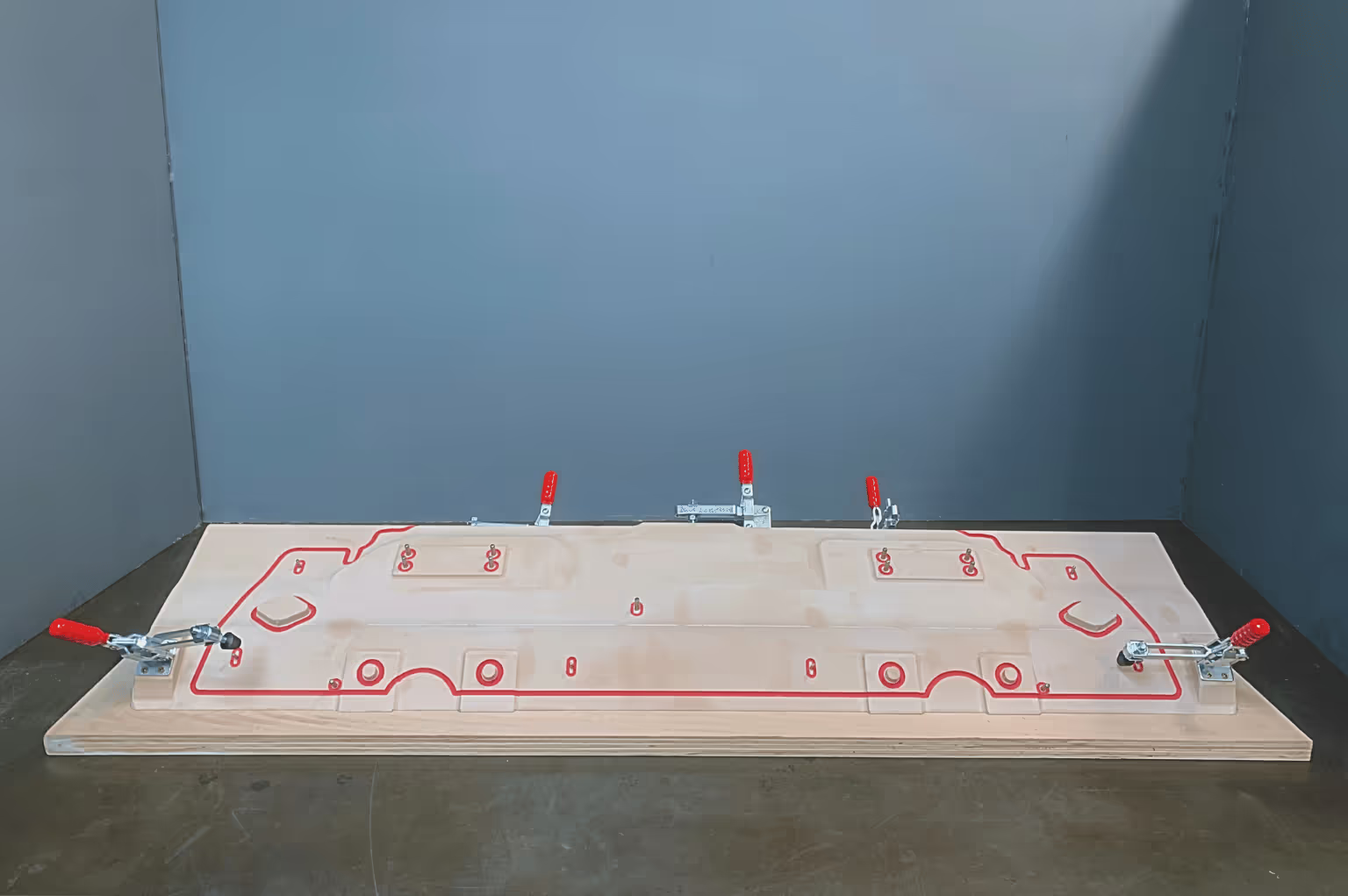
Assembly fixtures can make an otherwise-complicated process easy through intelligent design. Our first steps are to consider how different components need to fit together and what the real-world conditions that operators work with are. It’s very easy to get tripped up without experience – for example if you design expecting the components to be assembled to all be within a tight tolerance. If you then find the components an operator will work with have a wider tolerance and vary from part to part you can quickly find one a handful of parts fit the fixture.
All of this is thought about in the design phase by asking the right questions and coming up with a simple solution. Particularly with larger components we will often see if rationalising the design is possible, for example with an “egg box” skeleton construction, holding parts in critical areas but have free space outside those areas. This can really save huge cost with no negative impact on functionality.
Jigs & TRIM Fixtures | Tool Making Services
We have a long track record in working in the aerospace, automotive, mass transport, earth moving equipment and medical sectors. Geographically we have a wider customer base in the UK, Ireland mainland Europe and North America.
We can import all files and formats and daily work with STP, CATIA, XT and STL files. We run Powershape and Solidworks for technical CAD, and Geomagic Freeform for creative CAD (with haptic arm). We use Powermill for milling and Vectric for flat routing. In essence though we can take models from most formats and turn them into quality tooling, or create components from scratch.
We have 12 Hurco CNC machines - VMX30 (x2), 30s,
42i (x2), 50t, 50, 50i (x2), DCX 22i, VM10 and 10i; Romi d800; Maxicam M8 5 axis router/mill. We will shortly be commissioning a Roeders RXP501 HSM with 42K RPM spindle speed.
We can machine most metals up to 2200mm x 1600mm x 400mm 3 axis. Our 5 axis CNC can machine all model boards and some light aluminium work up to 2400mm x 1200mm x 500mm.
The vast proportion of our customers ask for Ureol/model board for prototyping and aluminium or steel dependant on the tooling. We work with a wide variety of model boards dependant on the application. Such is the volume of our purchasing for aluminium and model board we are very confident in our material costs on quotes and only charge a nominal handling charge on top. We do not mark up material costs.
Dependant on complexity of the job and capacity but we can go from receiving CAD data to delivery of tools and CNC fixtures in as little as 2 weeks, delivering ourselves where possible.
We’re certified to ISO 9001 but see this as a baseline to improve from and set our targets for quality higher than the standard requires.
We’ve been designing, machining and delivering thermoform tooling for 30 years and constantly reinvest in our capability to ensure we
stay ahead.
Who we work with…
Working alongside brands you know and love
We’ve helped the brands below with anything from creating parts for the next supercar, design a new plane seat or creating the next must-have chocolate. There’s never a dull day.
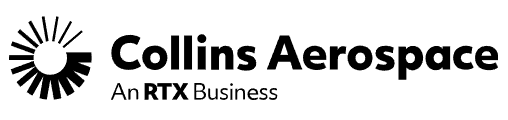
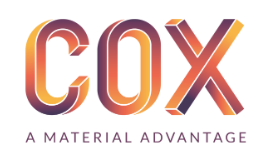
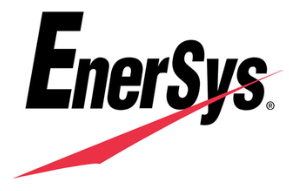
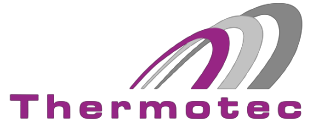
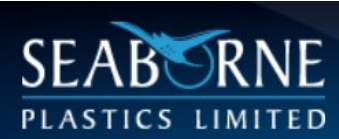
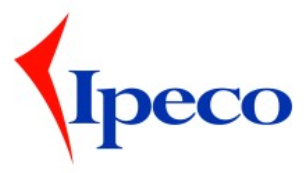
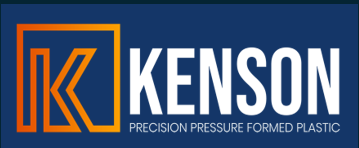
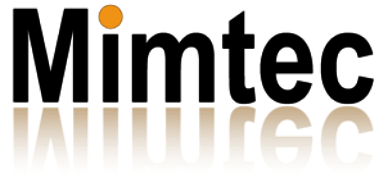
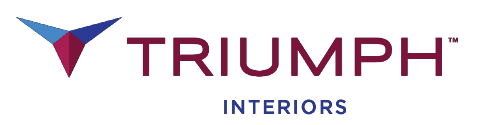
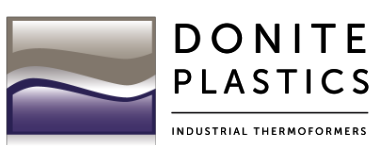
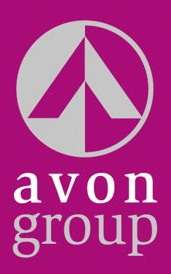
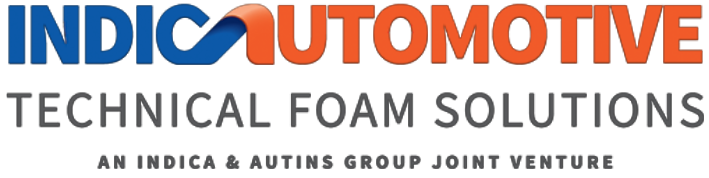
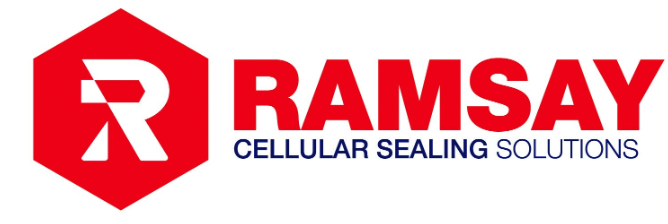
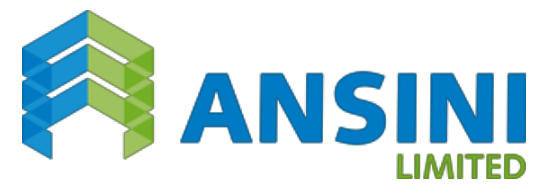
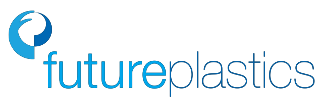
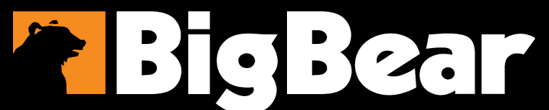

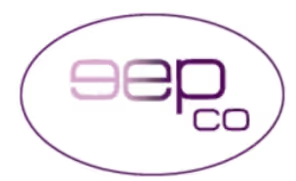
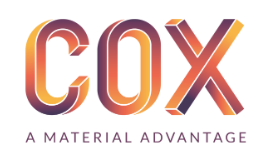